Torsten Strebel, Heimatforscher und Bürgermeister des Ortes Hanffabrik bei Nauen, stellte uns Material über die Entwicklung der regionalen Hanfindustrie zur Verfügung, das in seiner Ausführlichkeit auf unserem Blog nicht komplett wiedergegeben werden kann. In einem ersten Teil (Beitrag vom 4. Mai 2022) veröffentlichten wir Auszüge aus seiner Arbeit zur Entstehungsgeschichte des Ortes mit seiner Fabrik, in diesem Beitrag geht es um die damalige Art der Verarbeitung von Hanf und die Produktion von Hanffasern.
Teil 2: Hanfentholzung und Faseraufbereitung
Das Leben im Dorf wurde wesentlich durch den Rhythmus der Arbeit bestimmt. Jeden Morgen pünktlich um 7 Uhr rief eine Dampfsirene am Kesselhaus zur Arbeit, um 16:30 Uhr verkündete sie den Feierabend. Auch samstags wurde bis 13 Uhr gearbeitet […]
Der Hanf, der ursprünglich aus Persien stammt, ist eine einjährige ölhaltige Faserpflanze. Sie hat einen kräftigen Stiel von bis zu 3 Metern Länge. Die äußere Hülle des verholzten Stiels ist mit feinen, strapazierfähigen Fasern umgeben. […] Der Hanf wurde während der Samenreife maschinell gemäht und zum Trocknen in Bündeln aufgestellt, so wie man es auch von Getreide kennt.
Die Samenkerne mit einem Ölgehalt von 25 bis 30 Prozent wurden mit Spezialmaschinen ausgedroschen und zur Weiterverarbeitung an Ölmühlen verkauft.
Das sogenannte Hanfstroh, fingerstark und holzig, wurde für die Fasergewinnung aufbereitet. Dazu wurden die auf den Feldern getrockneten Hanfbunde aus den Scheunen oder von den Hanfmieten entnommen und kamen auf Gleisen in Waggons oder mit Fuhrwerken auf das Fabrikgelände bis an die großen Trockenöfen heran. Die massiven, circa 20 Meter langen Öfen entzogen durch Heißluft-Ventilatoren dem Hanf die letzte Feuchtigkeit.
Ein im Inneren des Ofens umlaufendes Förderband transportierte die Hanfbunde langsam durch den Trockner bis zu den am Ende der Anlage stehenden Knickmaschinen. Dort wurden sie vom sogenannten Einleger manuell aus dem Ofen entnommen, aufgeschnitten und für den Weitertransport zu den nachfolgenden Maschinen gleichmäßig ausgebreitet auf ein Fördertuch gelegt.
Die Knickmaschinen waren circa 10 bis 15 Meter lang, 0,85 Meter breit und bestanden aus einem massiven Untergestell, dem Walzenträger. In diesem liefen die sogenannten Riffelwalzen, die gerade oder wendelförmig verzahnt waren. […] Über ein Förderband gelangten die trockenen Hanfstiele langsam zwischen die Walzen und wurden von oben und unten mehrfach gebrochen. Es gab mehrere hintereinander angeordnete Walzenpaare mit unterschiedlicher Oberfläche, so dass bei weiterem Vortrieb der holzige Teil in viele kleine Stücke, die sogenannten Schäben (Abfälle), zerkleinert wurde und herunterfiel. Ein darunter laufendes Fördertuch fing die aussortierten Holzteile auf und transportierte sie ab. […]
Der geknickte und vom Holzanteil schon größtenteils befreite Hanf gelangte danach über ein Fördertuch in das sogenannte Schüttelwerk. Hier bewegten sich auf einer Fläche von 2,5 Quadratmetern aufrechtstehende Metallnadeln über ein Exzentergetriebe hin und her, so wurden die restlichen Schäben von der Faser ausgekämmt. Die Hanffaser gelangte danach per Förderband zum Ende der Produktionsstraße und wurde dort vom sogenannten Sortierer nach Güteklassen geordnet und zu separaten Haufen abgelegt. […]
Anschließend wurden die Fasern in einer speziellen Presse zu Ballen gepresst (diese hatten etwa die Größe wie die Strohballen in der Landwirtschaft), etikettiert und bis zum Abtransport trocken gelagert. Der Versand der fertigen Ware erfolgte mit Waggons der Deutschen Reichsbahn. Die Fabrik besaß dazu einen eigenen Gleisanschluss an der Bahnstrecke Berlin–Hamburg mit dem Bahnhof Bergerdamm. Das Gleisnetz war auf dem Fabrikgelände verzweigt, so dass die Waggons auch in die großen Scheunen ein- und ausgefahren und rangiert werden konnten. (…)
Wegen der erheblichen Staubentwicklung im gesamten Produktionsprozess waren an allen Maschinenabschnitten Absauganlagen vorhanden. […]
Die Fabrik betrieb auch ein eigenes Labor, in dem Versuche zur Steigerung der Ausbeute und Erhöhung der Qualität der Hanffaser unternommen wurden. Durch das sogenannte Rösten erzielte man zum Beispiel eine besonders feine, weiche Faser. Dazu wurden die bereits getrockneten Hanfbunde noch einmal für mehrere Tage in ein Wasserbecken getaucht und danach erneut zum Trocknen herausgestellt, bevor die Verarbeitung begann.
Anlagen wie die Schlosserei, Stellmacherei, Schmiede, Labor, soziale Bereiche wie das Bad für die Arbeiter und deren Familien, Betriebsküche, Wäscherei, Kantine, Saal für Veranstaltungen wurden zum großen Teil mit eigener Energieerzeugung betrieben. Die gesamten sozialen Einrichtungen konnten sowohl von den Werksangehörigen als auch von den Landarbeitern genutzt werden.
(Anmerkung Torsten Strebel: Die Beschreibung der Produktionsweise bei der Hanfentholzung und Fasergewinnung basiert auf schriftlichen Aufzeichnungen von Rudolf Keller, der bis zur Schließung des Betriebes als Schlosser und Mechaniker gearbeitet hat. Notiert von Siegfried Helbig im Juni 2019.)
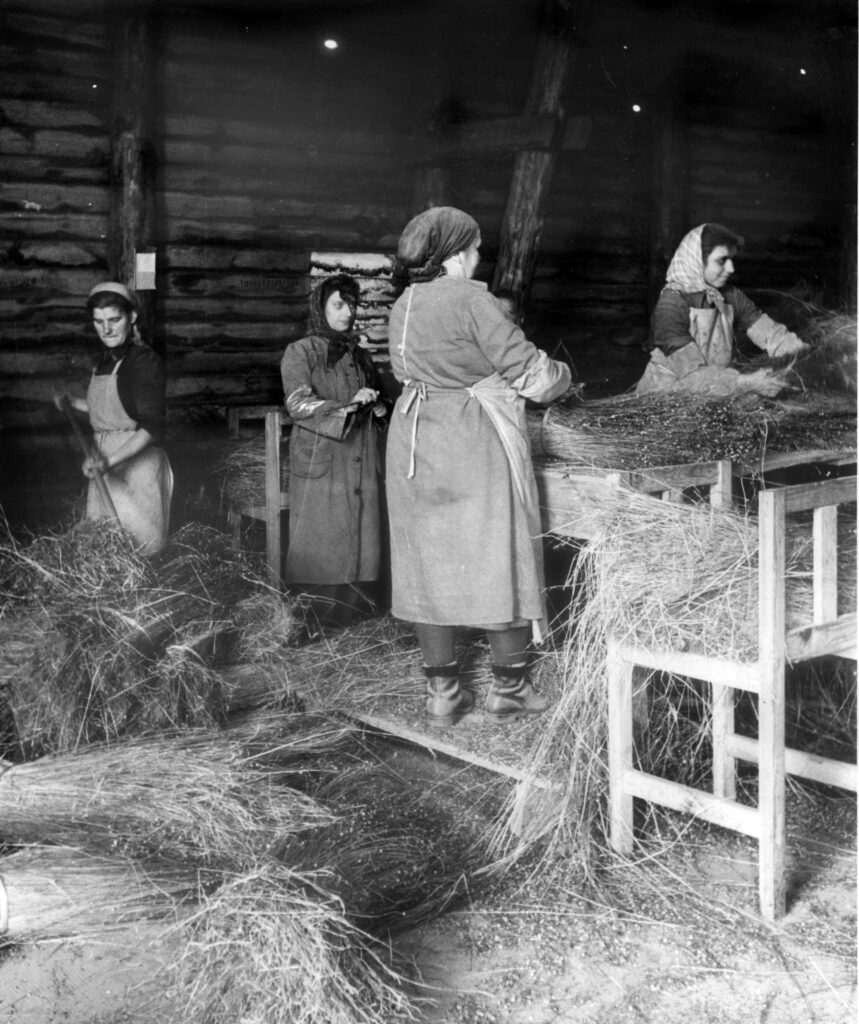
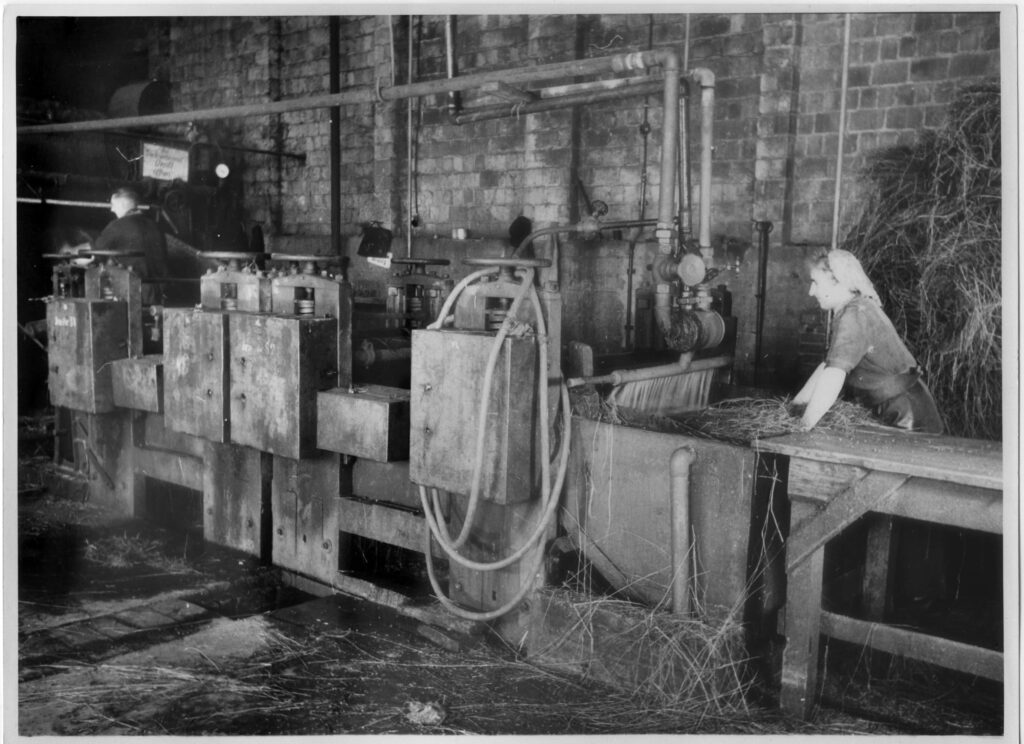
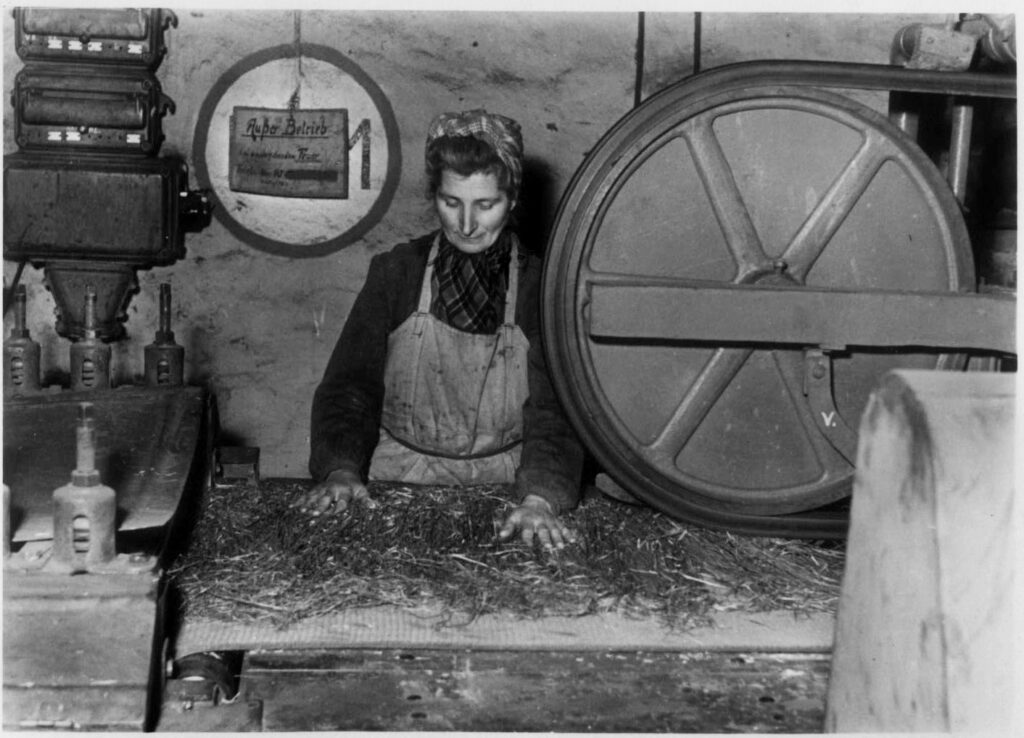
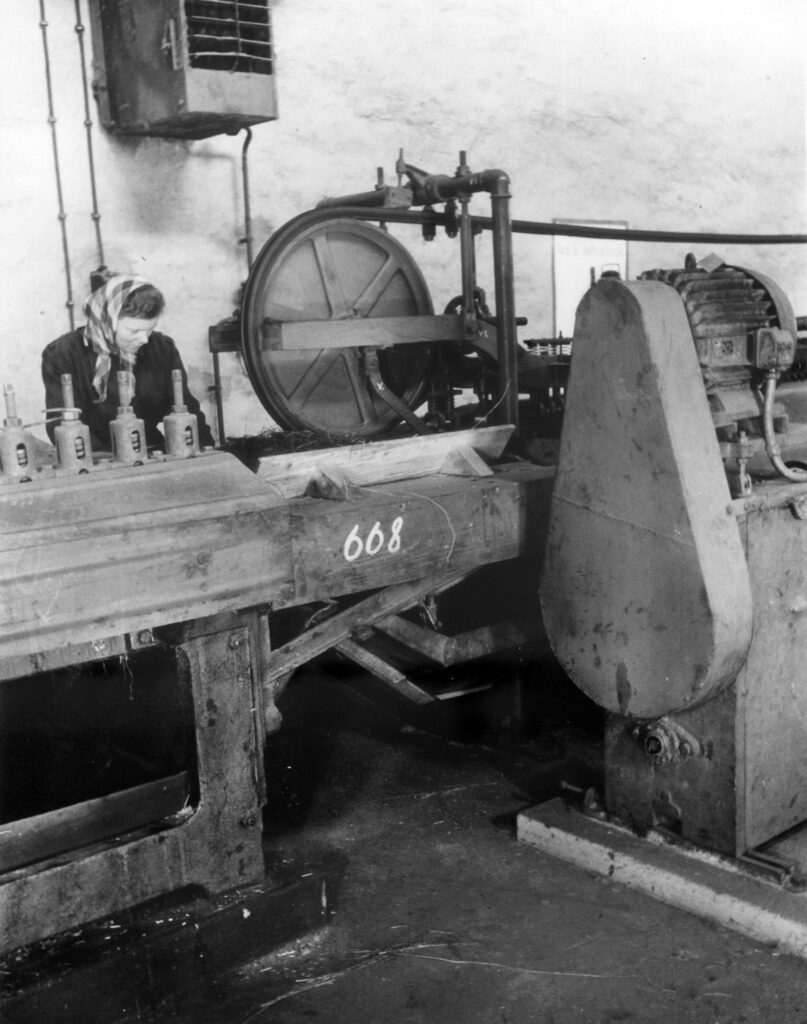
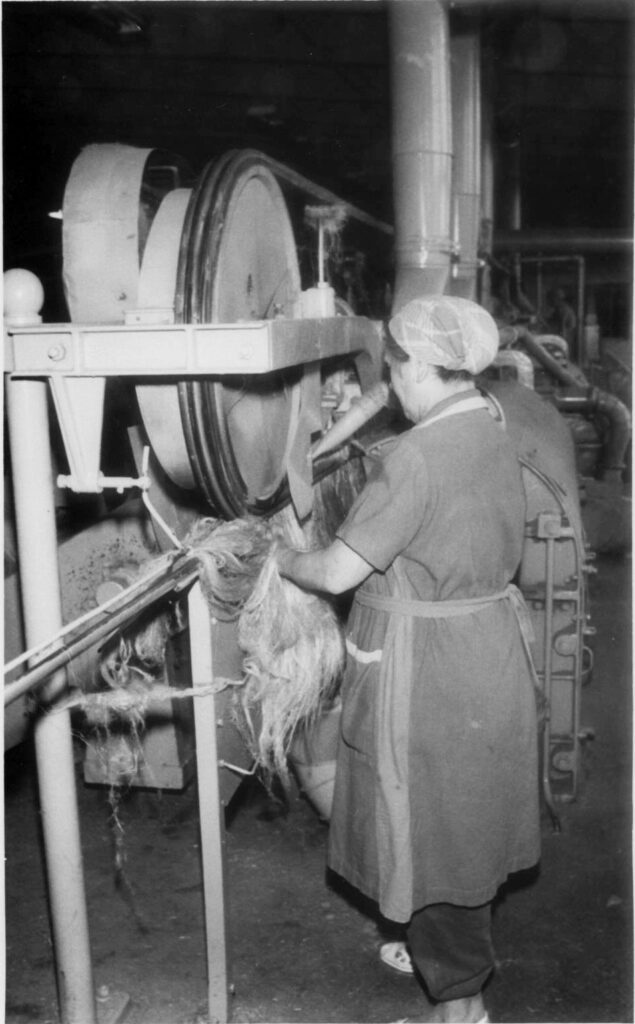
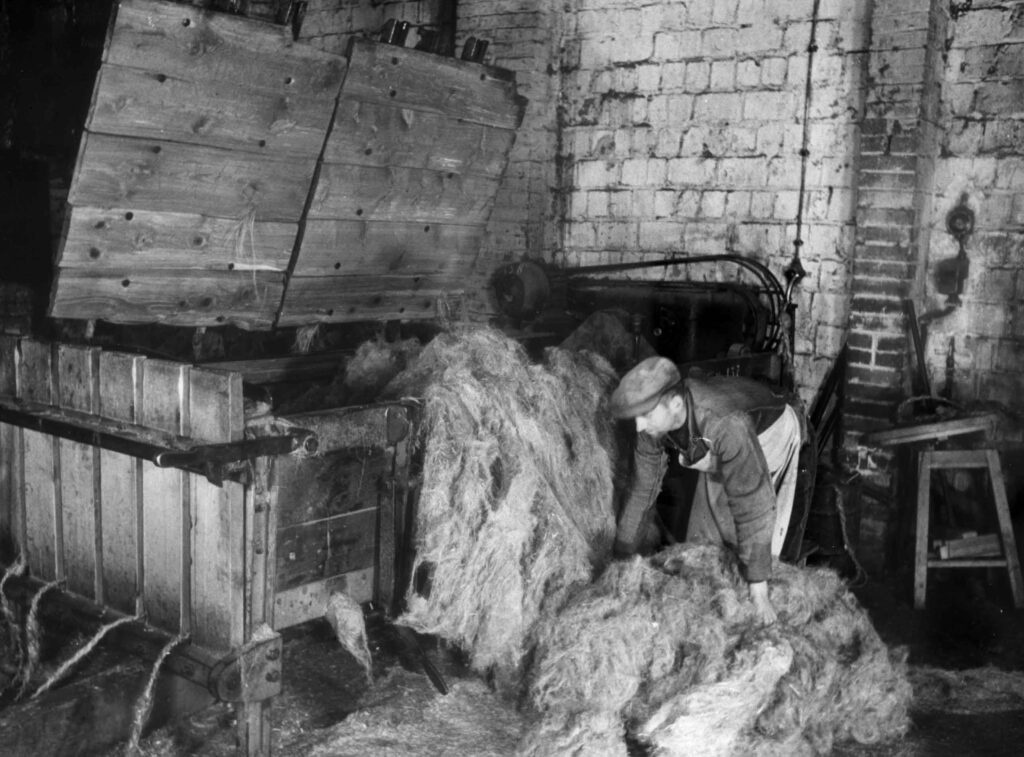
Fotos: Archiv Torsten Strebel